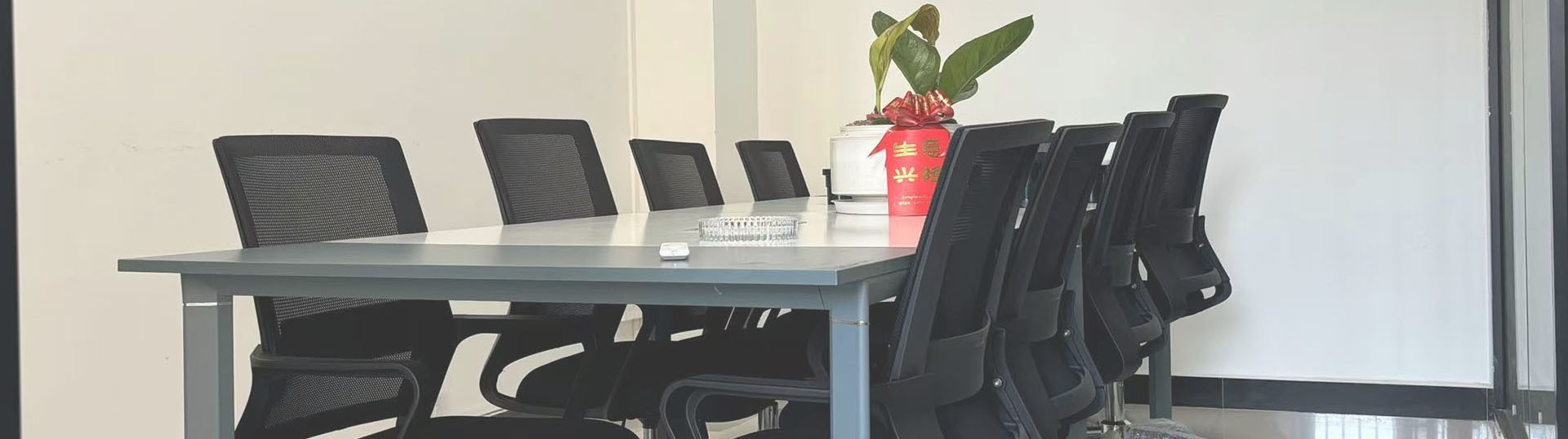
Volkan is dedicated to offering the best quality of custom machining services.
In the entire process of rapid prototypes making, after selecting the appropriate machining method (CNC machining, 3D printing, or vacuum casting), most prototypes require surface treatment. The purpose of surface treatment is to meet the corrosion resistance, wear resistance, decorative or other special functional requirements of the product. There are dozens of surface treatment processes for prototyping. Here are some commonly used surface treatment processes at Volkan.
1. Polishing
Polishing is the process of modifying the surface of a workpiece using flexible polishing tools and abrasive particles or other polishing media on the basis of polishing. Polishing cannot improve the dimensional or geometric accuracy of the workpiece, but is aimed at obtaining a smooth surface or mirror gloss, and sometimes used to eliminate gloss (extinction). The surface roughness of the workpiece after polishing process can generally reach Ra0.63-0.01 microns.
2. Plating
Electroplating is the process of using electrodes to apply current to attach metal to the surface of an object, with the aim of altering the surface characteristics or dimensions of the object. Electroplating is generally divided into two types- wet electroplating and dry electroplating. Wet method is commonly known as water plating, dry method is commonly known as vacuum plating.
Water plating is the process of using an electrode method to generate ion exchange and attach the plated metal to the surface of the workpiece. Vacuum plating, on the other hand, utilizes high voltage and high current to instantly vaporize the deposited metal into ions in a vacuum environment, which are then deposited onto the surface of the plated part. Water plating has good adhesion and does not require any further treatment in the later stage. Vacuum plating has poor adhesion and generally requires PU or UV coating on the surface. PC cannot be electroplated, and replica parts cannot be water plated, only vacuum plated. The color of electroplating is relatively monotonous, and common electroplating methods include chrome plating, nickel plating, gold plating, etc. Vacuum electroplating can solve the problem of rainbow colors. The surface effect of the workpiece must be polished to 1500-2000 grit sandpaper before water plating, so water plated workpieces are generally very expensive. The effect of vacuum coating polishing can be slightly inferior to 800-1000 grit sandpaper, so vacuum coating is relatively cheaper.
3. Anodizing
The anodizing treatment of metals is the formation of a protective oxide film on the surface of metals through the interaction with oxygen or oxidants, which prevents metal corrosion. Anodizing is divided into chemical anodigzing and electrochemical anodizing (i.e. anodic anodizing).
4. Sand blasting
It is powered by compressed air to form a high-speed jet beam that sprays materials (copper ore sand, quartz sand, diamond sand, iron sand, sea sand) onto the surface of the workpiece to be treated at high speed. Due to the impact and cutting effect of the abrasive on the surface of the workpiece, the surface of the workpiece obtains a certain degree of cleanliness and different roughness, improving the mechanical properties of the workpiece surface. Therefore, it improves the fatigue resistance of the workpiece, increases the adhesion between the workpiece and the paint coating, prolongs the durability of the paint film, and is also conducive to the leveling and decoration of the paint.